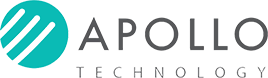
Have you ever encountered a situation where you want to just fuse a new optical fibre cable with an existing one, simply to make it longer or for the purposes of expanding your already existing fibre optic network? Many who are new to fibre optic technology but are familiar with the fact that optical fibre cables are made either of glass or plastic, might opt for fibre optic connectors for this purpose, thinking that the idea of fusing the optical cables is far-fetched and impossible. Well, this article is here is to tell you just the opposite!
Fusion splicing is a process that has been around for some time now with the concept developed from many subjects including heat transfer, optical waveguide theory, mechanical engineering, material science, and fluid mechanics. As the name suggests, the process is the joining of two optical fibres by creating a welded joint between them using a source of heat usually an electric arc or something like laser, gas flame or tungsten filament. It mainly involves stripping, cleaving, alignment and finally welding of the optical cables, followed by tests like insertion loss estimation, pull tension strength testing etc. to ensure reliability and mechanical strength.
Earlier the process was a hassle and there were no guarantees of the mechanical strength of the fused joint and the reliability of the optical connection through it. But with rapid advancements in technology, there emerged compact devices in the market called fusion splicers that perform the splicing process like a breeze with minimum insertion loss and long term reliability and mechanical strength. Fusion splicers, getting compact day by day and loaded with features like touch screens, USB interface, software updates etc., are made available at reasonable prices by manufacturers like Apollo Technology to benefit all those interested in having the power of fusion splicing.
Many latest splicing technologies are also being introduced in the market, for example the high precision Large Diameter Fibre (LDF) cleavers to deal with splicing of large diameter fibres. The cleavers are able to perform both flat and angled cleaving, providing high end solutions in many applications. Such equipment compliments existing fusion splicers and allow operators to achieve better results than ever before.
With much said about fusion splicers and the ease with which they are available in the market nowadays, let’s shed some light on the benefits of the process of fusion splicing itself as opposed to other methods of optical fibre interconnection like mechanical connectors. Fusion splicing offers the lowest insertion loss, lowest back reflection (optical return loss ORL), while being the most compact and having the highest mechanical strength. Fusion splicing seals the optical fibres to dust and other contaminants ensuring that they do not interfere in the optical path. Moreover, the optical fibres passed through the fusion splicing process can withstand extremely high temperatures and hence meet fire code restrictions with ease. Finally, splicing is more economical in crowded conduits where there is no/ little space for additional connectors.
The players of telecommunications industry, whether it be cable TV vendors, telephone companies, media providers etc., all are scrambling to strengthen, enhance, and make their optical networks more reliable and beef up their businesses, which in turn puts ever-growing requirements on modern tools, equipment and technology in the field of optical fibre networks. With the need of increased cabling installation, the demand of more reliable and advanced equipment for fusion splicing is also becoming an essential requirement. Manufacturers of fusion splicers like Apollo Technology have played a key role in bringing the technology of fusion splicing into the hands of these players at an affordable price, and are putting effort to progress this technology.